Work-In-Process (WIP) Tracking
Work-In-Process Tracking Solution Transforms Leading Equipment Component Manufacturer’s Industrial Manufacturing Process

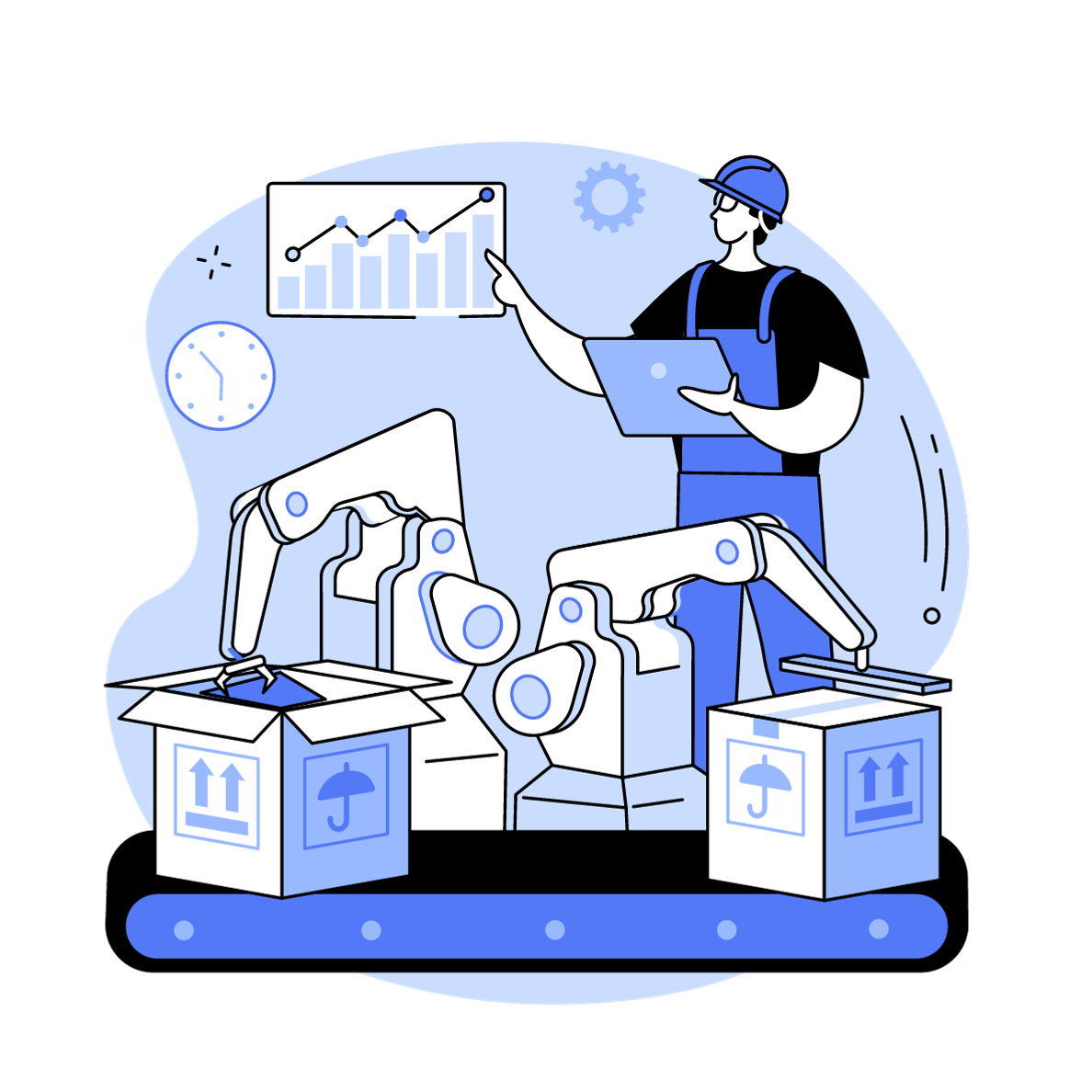
The Challenge: Limited Visibility Into Complex Fuel Injector Assembly
For the world’s leading industrial equipment manufacturer, keeping track of certain aspects of production can be a challenge, but it is a must for ensuring operational efficiency. However, the manufacturing of fuel injectors poses a significant challenge.
As their most complex assembly, the fuel injector manufacturing process encompassed a 20-step procedure involving multiple parts and pieces. Visibility into the work-in-process was minimal, as staff relied on pen and paper to track production status.
This manual tracking method lacked accuracy and vital information, leading to the following:
– Overtime hours for employees
– Rust issues on parts
– An increase in scrapped components
The Solution: Radiant’s Work-In-Process (WIP) Tracking
The manufacturer deployed Radiant’s Work-In-Process (WIP) Tracking Solution to address these challenges. Implementation involved attaching Radiant’s T21 beacons to the trays that moved parts through production.
By leveraging the Floor Operations Module in Radiant’s IoT Platform, specifically designed for floor operators, they could gain real-time visibility into the number of parts at each stage in the process.
Tangible Results and Business Impact
The implementation brought significant improvements to the fuel injector manufacturing process and provided benefits such as:
1. Tracking utilization of critical machines involved in production, including parts wash stations – a chokepoint in the process
2. Detection of when conveyor belts are empty, preventing slowdowns in production
3. Ease of locating empty containers
4. Enhanced visibility in the company’s ERP system and more efficient order fulfillment
5. User-friendly system with automated reports emailed to shift supervisors, eliminating the need for manual reporting
6. Other departments have begun evaluating the use of the WIP Asset Tracking Solution
Additional Considerations
Despite the rough, heavy metal environment occasionally causing damage to the beacons, Radiant’s flexible approach enables them to evaluate alternative tracking methods, such as autoclavable tags.
Transforming the Business: The Client’s Perspective
With the successful implementation of Radiant’s WIP Tracking Solution, the leading Equipment Manufacturer has experienced a significant decrease in operational costs, increased productivity and efficiencies, and improved customer satisfaction.
The company continues to transform its business, embracing IoT solutions to streamline and optimize its manufacturing processes. The newfound transparency provided by Radiant has empowered the organization to tackle ongoing challenges head-on, further solidifying its position as a global leader in industrial manufacturing.
Are your industrial manufacturing plants ready to:
- Enhance visibility into complex manufacturing processes?
- Track utilization of critical machines and equipment?
- Increase productivity of your industrial manufacturing facilities?
- Eliminate the need for manual reporting?
- Automatically monitor and manage assets?
If you answered “yes” to any of the above and want to learn more about our WIP asset tracking solutions or life safety solutions, please request a demo below.